Wednesday, May 31, 2023
Interview with Philippe Ciniello, Business Development Manager LATI Industria Termoplastici S.p.A.
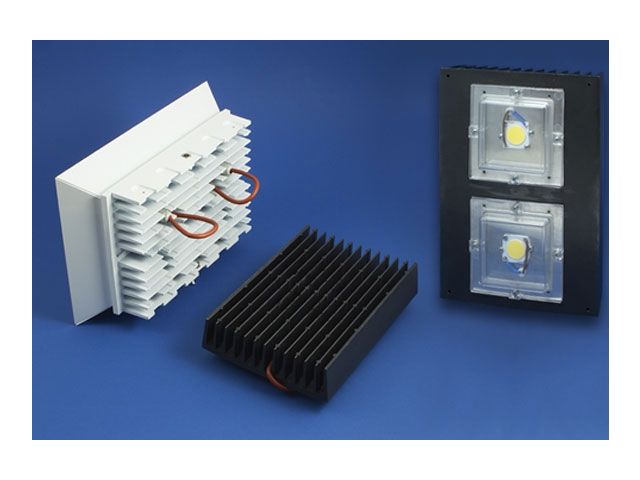
In the run-up to its participation at FPC on October 2 and 3, plastics manufacturer LATI SPA, represented by Philippe Ciniello (Business Development Manager), tells us more about its expertise and solutions for the circular economy.
What is LATI SPA's main mission?
LATI is an Italian manufacturer of highly technical thermoplastic compounds for injection molding in particular, and a major leader in Europe. We are present worldwide through our own subsidiaries and local partners, marketing our products in Europe, Asia and the Americas. We produce around 40,000 tonnes of compounds at our two production plants in Italy, north of Milan, but also via subcontracting partners for local production in China and the USA.
Today, LATI has sales of almost €200 million and over 250 employees.
The company's product offering is based on 2,500 standard and customized formulations, mainly serving the electrical and household appliance, industrial, automotive and rail transport sectors.
LATI already has a strong reputation in the polyamide market, with products such as PA6, PA66 and PA6.66 under our own LATAMID and KELON brands.
Finally, 5 years ago, we set up an entity specifically dedicated to the development of formulations for the additive manufacturing sector, more specifically 3D printing by wire deposition "FDM & FFF". Known as Lati3DLab, this team combines the skills of R&D, the laboratory, production and the field sales force.
Ultimately, we support our customers in their developments by bringing our expertise in highly technical thermoplastics to bear, from design to implementation.
Without revealing everything, could you tell us about one of your innovative solutions that will surprise our visitors at FPC?
Metal replacement is still a hot topic on the market, with compounds featuring very high mechanical modulus. Today, however, there is a growing need for plastic parts capable of electrical conductivity or heat dissipation as an alternative to aluminum and its alloys.
Radiators and heat sinks molded directly in plastic are now possible with our LATICONTHER compounds.
How do your solutions/developments fit into a circular economy approach?
When LATI was founded in 1945, Cosimo Conterno set up a plant to sort and recycle the plastic debris left over from the war. Since then, we have continued to work towards a sustainable, circular economy by offering products derived from recycling or natural resources. Our LATIECO and LATIGEA ranges have a very low ecological impact, reducing their carbon emissions by 15 to 90% compared with their virgin, fossil-based equivalents.
Naturally, our means of production and industrial processes are continually renewed and modernized to become and remain ever more eco-responsible. LATI had committed to reducing its greenhouse gas emissions by 50% between 2020 and 2025. This was achieved in 2021, with a 60% reduction in scopes 1 and 2.
LATI is an energy-intensive company. We are therefore committed to purchasing and producing "green" electricity. As of 2020, we have invested in photovoltaic panels on our main manufacturing site, with a capacity of 117 kWatt. This will reduce our CO2.eq emissions by 60 tonnes a year, the equivalent of planting 1,827 trees.